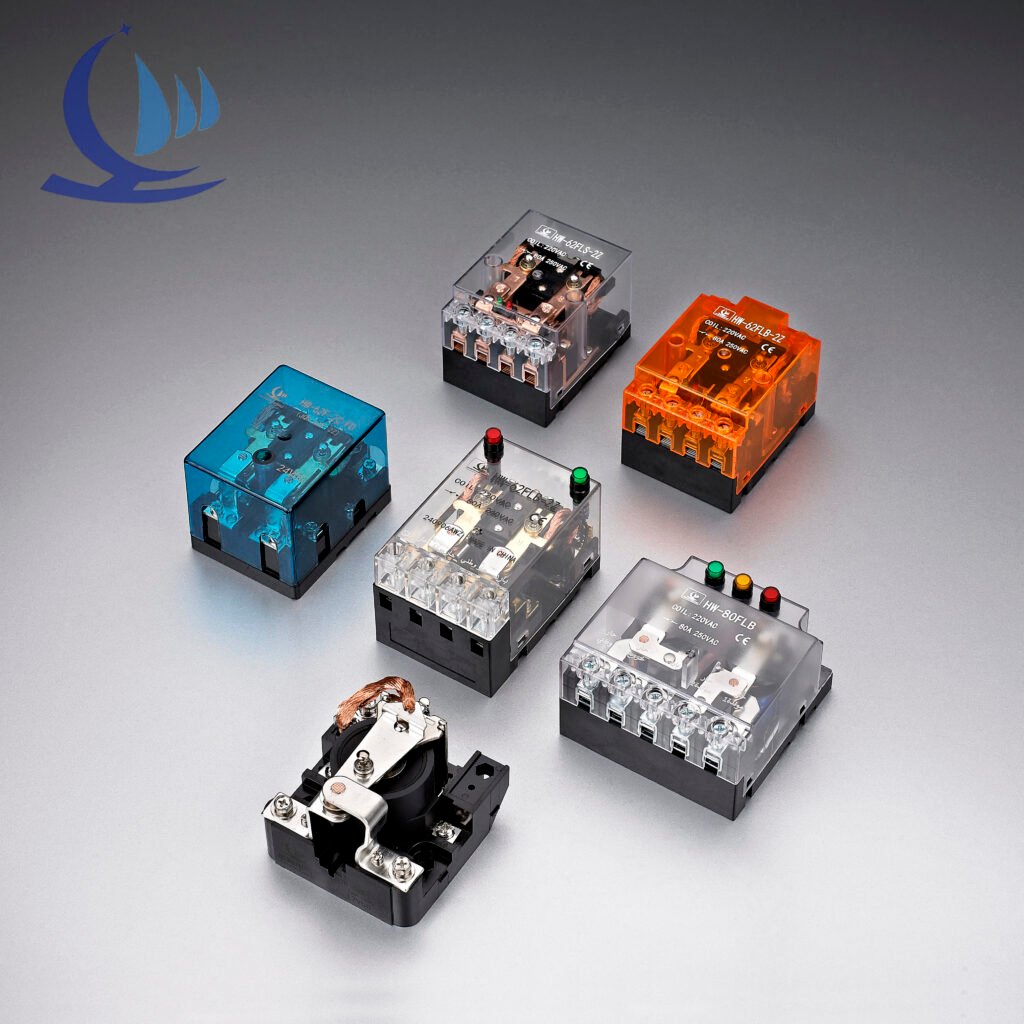
Let’s take a closer look at small relay products
Working principle of small relay
A small relay is an electrical switch that operates using the principle of electromagnetic induction to control the on and off states of a circuit. It typically consists of four main components: a coil, an iron core, an armature, and contacts. When the coil is energized, current flows through it, generating a magnetic field. This magnetic field pulls the armature, causing it to move and change the state of the contacts—either opening or closing the circuit.
In simpler terms, a small relay allows a small control current to manage a larger load current. For instance, in a 5V relay, the input only requires a 5V low-voltage signal to operate, but it can switch much higher load voltages. This makes small relay incredibly useful in various automatic control systems such as household appliances, industrial equipment, and even automotive applications.Imagine your home air conditioner: when you set the temperature on your remote control, a small signal is sent to a small relay inside the unit. This small relay then controls the larger current needed to power the compressor and fan motors—allowing you to cool your room without directly handling high-voltage circuits.

What is the difference between the normally open contact and the normally closed contact of a small relay?
In any HW-14F-1Z small relay, contacts are divided into two types: normally open (NO) and normally closed (NC). These terms describe what happens when the small relay coil is not energized.
- Normally Open (NO): When no power is applied to the coil, this contact remains open—meaning no current flows through. Once the coil is energized, however, it closes, allowing current to pass.
- Normally Closed (NC): The opposite of NO contacts. When no power is applied to the coil, this contact stays closed—allowing current to flow. But when the coil is energized, it opens and cuts off the current.
This distinction allows for flexible design in various applications. For example, in safety-critical systems like fire alarms or emergency stop systems, normally closed contacts are often used. If there’s a power failure or system fault, these contacts will automatically open and break the circuit—ensuring that machinery stops or alarms are triggered even if something goes wrong with power supply.
Advantages and disadvantages of small relay types
There are several types of small relay available on the market today, each with its own set of strengths and weaknesses depending on your application needs:
Electromechanical Relay
- Advantages:
- High reliability due to their simple mechanical design.
- Low cost.
- Capable of handling high-power loads.
- Disadvantages:
- Since they rely on moving parts (like an armature), they can wear out over time.
- Slower response times compared to other types because of physical movement.
Electromechanical relays have been around for decades and are still widely used in environments where cost-effectiveness and robustness are key factors—like HVAC systems or automotive applications.
Solid State Relay
- Advantages:
- No moving parts means longer life expectancy.
- Faster response time compared to EMRs.
- Silent operation (no clicking sounds).
- Disadvantages:
- Generally more expensive than electromechanical relays.
- They can generate heat during operation and often require heat sinks for proper cooling.
Solid-state relays are ideal for applications requiring frequent switching without wear and tear—such as industrial automation systems where downtime must be minimized.
Reed Relay
- Advantages:
- Compact size makes them perfect for space-constrained designs.
- Fast switching speeds make them suitable for low-power applications like signal switching in telecommunications or instrumentation.
- Disadvantages:
- Not as durable as other types due to their delicate internal components.
- Unsuitable for high-power loads.
Reed relays are often found in precision electronics where fast response times are critical but power requirements are minimal.Each type of relay has its place depending on your specific needs. For example, if you’re building an industrial control system that requires high-speed switching with minimal maintenance, a solid-state relay might be your best bet. On the other hand, if you’re working with simpler home automation projects where cost is a concern but speed isn’t critical, an electromechanical relay could be more appropriate.
Structural Differences Between Different Types of Small Relay
Small relay come in various types, each with distinct structural differences that influence their performance, durability, and suitability for different applications. Understanding these structural distinctions can help you select the right relay for your specific needs.
Electromechanical Relays
Electromechanical relays are the most traditional type of relay. They rely on mechanical moving parts, such as armatures, springs, and physical contacts, to switch a circuit. When the coil is energized, it generates a magnetic field that pulls the armature, causing the contacts to either open or close. This mechanical movement is simple but comes with inherent limitations:
- Wear and Tear: The constant movement of mechanical parts results in wear over time, reducing the relay’s lifespan.
- Slower Response: Due to the physical movement involved, electromechanical relays have slower switching speeds compared to other types.
Despite these drawbacks, electromechanical relays are still widely used due to their cost-effectiveness and ability to handle high-power loads. They are often found in industrial machines and automotive applications where robustness is key.
Solid-State Relays
Solid-state relays differ significantly from electromechanical relays because they contain no moving parts. Instead of mechanical contacts, SSRs use semiconductor components, such as transistors or bidirectional thyristors, to perform electronic switching. This structure offers several advantages:
- Fast Response Time: Since there are no moving parts, SSRs can switch much faster than electromechanical relays.
- Silent Operation: Without mechanical components clacking together, SSRs operate silently.
- Longevity: The absence of mechanical wear extends their operational life significantly.
However, solid-state relays do have some downsides:
- Heat Generation: SSRs can generate heat during operation and often require heat sinks or other cooling mechanisms to prevent overheating.
- Higher Cost: They tend to be more expensive than electromechanical relays due to their advanced technology.
SSRs are ideal for applications that require frequent switching without the risk of mechanical failure—such as in industrial automation systems or temperature control units.
Reed Relays
Reed relays have a unique structure that includes a magnetic reed switch sealed inside a small glass tube. When the coil is energized, the magnetic field causes the reed contacts to close and complete the circuit. This design offers several benefits:
- Compact Size: Reed relays are much smaller than both electromechanical and solid-state relays, making them suitable for space-constrained applications.
- Fast Switching Speed: Like SSRs, reed relays can switch quickly due to their lightweight internal components.
However, reed relays are not without their limitations:
- Limited Power Handling: They are not designed for high-power loads and are better suited for low-power signal switching.
- Fragility: The delicate glass enclosure makes them more prone to damage compared to other types of relays.
Reed relays are commonly used in telecommunications equipment and other low-power applications where size and speed are critical factors.
Application scenarios of small relay in power protection field
Small relay play a crucial role in power protection systems across various industries. They help safeguard equipment from overloads, short circuits, and other electrical faults by automatically disconnecting circuits when necessary.
Overload Protection
Overload relay are designed to protect equipment from damage caused by excessive current. These relay monitor the current flowing through a motor or other device and trip the circuit if an overload condition is detected. For example:
- In industrial equipment like conveyor belts or pumps, an overload relay will disconnect power if it senses that the motor is drawing too much current—preventing overheating or damage.
Overload protection is essential in any system where motors or heavy machinery are used because it helps extend equipment life and reduces downtime due to repairs.
Contactor Relay
A contactor relay is a heavy-duty relay specifically designed for switching high-power loads. It operates similarly to an electromechanical relay but on a larger scale. Contactors are commonly used in industrial settings where large motors need to be started and stopped frequently:
- For example, in large HVAC systems or manufacturing plants, contactors control motors that drive fans or compressors. These contactors often come equipped with built-in overload protection to ensure safe operation under heavy loads.
The key advantage of contactors is their ability to handle higher currents and voltages than standard relays—making them indispensable in high-power applications.
Fridge Relay and Overload Protector
In household appliances like refrigerators, small specialized relays play an important role:
- The start relay helps initiate the compressor motor when cooling is needed.
- The overload protector ensures that the compressor does not overheat or become damaged by excessive current draw.
These components are relatively inexpensive; for example, you can find refrigerator start relay kits on Amazon priced between $7.48 and $12.89. Despite their low cost, these relays provide critical protection for one of the most expensive components in your fridge—the compressor.