
Industrial Relay Contact Selection Analysis
In modern industrial automation systems, industrial relay contact serve as essential bridges for electrical control. At the heart of every relay are its contacts-the components responsible for making or breaking the circuit. The performance and reliability of these contacts directly impact the stability and safety of the entire system. Many relay failures can be traced back to contact issues such as sticking, arcing, or poor conductivity.
Therefore, understanding the structure, material selection, lifespan factors, and optimization methods for Industrial relay contact is vital for buyers, engineers, and maintenance personnel. This article provides a comprehensive overview of industrial relay contacts, helping you select the right product and improve your equipment’s overall reliability.
Basic Structure and Types of Industrial Relay Contact
Basic Structure: Relay contacts consist of moving and stationary elements that open or close circuits through mechanical action.
Types:
- Normally Open (NO): Open when de-energized, closed when energized; commonly used for power control.
- Normally Closed (NC): Closed when de-energized, open when energized; often used in safety circuits.
- Changeover (CO): Switches between NO and NC; suitable for multi-way control.
Symbols: Illustrate common schematic symbols for each contact type.

Comprehensive Comparison of Contact Materials and Performance
The material of Industrial relay contact is crucial for their durability, conductivity, and resistance to wear, welding, or corrosion. Here is a comparison table of common relay contact materials, their characteristics, suitable applications, and drawbacks:
Material | Description | Best For | Drawbacks |
---|---|---|---|
Silver Nickel (AgNi) | Silver alloyed with ~10% nickel; good conductivity and durability | General-purpose, resistive loads | Oxidizes at high temperatures |
Silver Cadmium Oxide (AgCdO) | Excellent anti-welding, handles high inrush currents | Inductive loads, motors | Phased out due to cadmium toxicity |
Silver Tin Oxide (AgSnO₂) | High resistance to welding and arcing, long life | High inrush, capacitive/inductive loads | Can wear faster under DC loads |
Hard Silver (Ag) | Silver mixed with copper/nickel for hardness | General-purpose relays | Oxidizes at high temperatures |
Silver Tin Indium Oxide (AgSnOinO) | Improved version of AgSnO₂, even better for inrush currents | Power circuits with large surges | Less common, more expensive |
Tungsten (W) | Extremely hard, excellent arc resistance, high melting point | High-power, high-voltage applications | Expensive, lower conductivity |
Gold Plating (10μm Au) | Thin gold layer, excellent for low-power, corrosion resistance | Low-power, signal circuits | Wears off after ~1 million cycles |
Gold Flash (3μm Au) | Very thin gold layer for storage protection | Low-power, seldom-used relays | Less durable, wears off easily |
Palladium (Pd) | Does not oxidize, very low electrical noise | Low current, signal switching | Limited to ~5A, lower conductivity |
Selection Tips:
- For high power applications, use Silver Nickel, Silver Cadmium Oxide, or Tungsten for better resistance to welding and burnout.
- For inductive or motor loads, Silver Cadmium Oxide and Silver Tin Oxide offer the best performance.
- For low power or signal switching, choose Gold-plated or Palladium contacts for reliable, corrosion-resistant connections.
- Consider RoHS and environmental regulations, as some materials (like AgCdO) are being phased out in favor of safer alternatives.
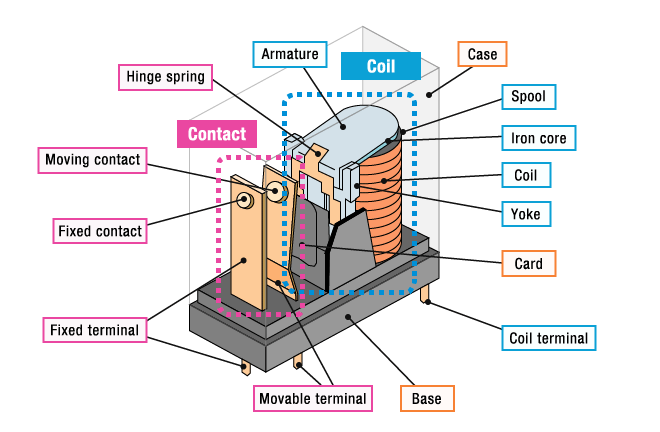
Key Factors Affecting Contact Life
Electrical Factors: Current and voltage levels, type of load (resistive, inductive, capacitive) directly influence contact wear and arcing.
Mechanical Factors: Frequency of operation, spring pressure, and contact gap affect reliability.
Environmental Factors: Temperature, humidity, dust, and corrosive gases can accelerate oxidation and wear.
Arcing and Sparking: Contact opening/closing can generate arcs, leading to erosion and material transfer.
Common Contact Failures and Prevention
Sticking/Welding: Caused by high current or arcing, making contacts fuse together.
Erosion: Repeated arcing forms pits and black oxides on contact surfaces.
Increased Contact Resistance: Due to contamination or oxidation, raising circuit losses.
Preventive Measures:
- Select appropriate contact material (e.g., AgSnO₂ for anti-sticking).
- Add RC snubber circuits to suppress arcing.
- Regular maintenance and cleaning of contact surfaces.
Contact Protection Technologies and Life Extension Methods
RC Snubber Circuits: Parallel resistor-capacitor networks absorb voltage spikes from inductive loads, reducing arcing.
Arc Suppression Devices: Magnetic blowouts or air gaps extend contact life.
Optimized Design: Proper spring force and contact gap reduce mechanical wear.
Selection Advice: Match contact material and type to load characteristics and application environment.
Application Case Studies
Lighting Control: High current, frequent switching; requires wear-resistant contacts.
Motor Control: Inductive loads generate high inrush and back EMF; needs anti-welding materials and protection circuits.
Automation Equipment: Low current, high frequency; needs low-resistance, wear-resistant contacts.
FAQ
Q: Why do contacts get burned?
Arcing caused by switching high currents or inductive loads leads to surface burning of contacts.
Q: How to prevent contact sticking?
Use anti-sticking materials (such as AgSnO₂) and install RC snubber circuits to effectively prevent sticking.
Q: What is the typical lifespan of contacts?
It depends on load type, working environment, and materials, usually ranging from 100,000 to several million cycles.
Q: How to choose contact materials?
Select suitable materials such as silver alloys or silver tin oxide based on load characteristics, switching frequency, and cost.
Q: Why do contacts heat up?
Excessive contact resistance or high current causes contacts to heat up.
Industrial relay contact, though small, are critical to the reliability and lifespan of industrial control systems. By carefully selecting contact materials, designing appropriate protection circuits, and performing regular maintenance, you can significantly extend relay life and reduce downtime due to contact failures.
For different application scenarios, consider load type, current, voltage, and environmental conditions to choose the most suitable Industrial relay contact type and material. Combining practical experience with the right technical knowledge will help your business achieve higher efficiency and lower maintenance costs. We hope this guide assists you in making informed decisions for relay contact selection and application.